オーストラリア国家衛生安全委員会
安全設計指針(案)
序文
この安全設計指針は、2003年の委託研究討議報告書に対する利害関係者の意見と国家規格作業グループが特定した課題にそって作成され、ビル・建造物、工場設備、材料及び作業システムについての安全設計の実用化に関する明確な定義と実例を提供する。 また、国家規格に基づいての安全設計責任について設計者を支援する。 指針は、今後、主要な設計専門家及び労働安全衛生委員会(NOHSC)メンバーの代表を含む専門のレファレンス・グループによって検証された後、適用される。
この指針は、全国労働安全衛生委員会事務局が読みやすく、正確で、アクセスしやすくし、関連性のある資料を開発するため利害関係者及び利用者と連携する観点からさらに検討中である。
意見提示
この指針に対しあなたができる貢献は、全国労働安全衛生委員会事務局が安全設計指針の開発を周知するために行っている協議への重要な参画である。 我々は、資料の中で具体的な質問(又は、注意)を提示して、あなたの意見の提供を求めている。
この指針について意見を提示するには、労働安全衛生委員会事務局の安全設計チームに連絡して頂きたい。 郵便、ファクシミリ、電話又はメールによって意見を提示できる(電子コピーが望ましい):
郵便の宛先: 安全設計チームリーダー、労働安全衛生委員会、GPO Box1577 Canberra ACT 2601
電話番号: (02) 6279 1142 FAX番号: (02) 6279 1190
Eメールアドレス: safedesign@nohsc.gov.au
すべての意見は2005年2月28日月曜日の業務終了以内に提出して頂きたい。受理したすべての意見は検討される。 守秘義務が要求されない限り、すべての寄稿は公文書として扱われる(労働安全衛生委員会ウェブサイト及び労働安全衛生委員会会議用の書類の出版を含む)。
要旨
この指針は、工場設備、建設工事、材料及び作業システムを中心に設計段階でハザードを除去するための方針と手順上の枠組みの開発に使用できる指針を設計者、メーカー、納入業者、輸入業者及び使用者に提供する。
また、指針は、安全設計を支える原則とこれらの原則が実際に工場設備、建設工事、材料及び作業システムの重点分野にどのように適用されるかを説明する。
安全設計方針と手続き上の枠組みに適用されるそれぞれの原則は、それらが指針にどのように採用されるかが議論される。
安全設計の原則は:
- 原則 1: 管理又は影響力―安全設計の責任は、製品、作業項目又は作業システムの設計において管理又は影響力を持つ関係者又は個人にある。
- 原則 2: 設計された製品のライフ・サイクル―ライフ・サイクルアプローチの適用は、設計された製品の安全設計への鍵である。
- 原則 3: 組織的リスク管理―組織的リスク管理過程は実行にあって必要である。
- 原則 4: 安全設計のための知識及び能力―設計者又は安全設計への管理及び影響力を有する者によって示されるか、又はアクセスされる。
- 原則 5: 主要な情報の転送及びフィードバック―すべてにかかわる情報の相互転送及びフィードバックが安全設計アプローチに必要である。
また、この指針は、工場設備、建設工事、材料及び作業システムに安全設計を適用する多くのケーススタディを提供する。
1. 序論
安全設計に関するこの指針は、「設計段階でハザードを取り除く」という労働安全衛生委員会の戦略的優先策を支持する。指針は、設計者、メーカー、納入業者、輸入業者、使用者、その他の利害関係者に設計段階でハザードを除去する方法についての情報及びアドバイスを提供することを意図している。
1.1 目的
この指針の目的は、設計者、メーカー、納入業者、輸入業者、使用者に設計段階でハザードを取り除くために、方針と手続き上の枠組みの開発に、工場設備、建設工事、材料及び作業システムを中心として活用できる指針を提供することである。
それは、枠組みに適用されるそれぞれの原則を記述する。それには以下を含む:
- 製品、作業項目、作業システムの設計を管理するか又は影響力を持つ者の責任
- ライフサイクル・アプローチ
- 組織的危険管理
- すべての関係情報の相互転送及びフィードバック
また、工場設備、建設工事、材料及び作業システムに安全設計を適用する多くのケーススタディをも提供する。
1.2 指針の概要
この指針の第1の目的は、定義を提示し、なぜ安全設計がオーストラリアの状況で重要なのかを説明する。第2に、基礎となる安全設計の原則について、これらの原則はどのように工場設備、建設工事、材料及び作業システムの領域に実際に適用されるかを説明する。
1.3 安全設計とは
安全設計は、安全について明確に「川下」に影響を与える「川上」の決定に関するものである。
設計段階においてハザード除去、つまり安全設計は、「根源において」安全衛生へのハザードの排除及びリスクの制御に(作業場を構成、作業で使用又は該当する項目の計画及び設計の出来るだけ早期に)関与する。リスクよりも設計段階におけるハザードの排除の考え方が優先される。ハザードが隔離されるならば、ハザードにさらされる人々の機会が(したがって、作業場のリスクも)なくなるであろう。
これらの事項(設計された製品として広く定義された項目)は、以下を含む:
- 作業施設(ビル)、建造物、他の建設工事及び構造材料
- 工場設備(機械、設備、器具、及び道具)
- 材料
- 作業方法と作業システム(包装を含む)
設計された製品は、ライフサイクルの中で、発想、生産され、存在し、終焉を迎える。設計された製品(図1参照)のライフサイクルは、設計段階でハザードの除去及び又はリスク制御の枠組みを提供する安全設計の重要なコンセプトである。
設計された製品は以下の通り:
- 組み立てられるか又は製造される。
- 供給するか又は設置される。
- 稼動される、使用及び又は操作される。
- 維持される、修理される、清掃され及び又は変更される。
- 使用廃止される、壊され及び又は解体される。
- 処分されるか又は再生される。
設計された製品のライフサイクルにおける安全設計アプローチは、設計、製造・工事方法及び安全性を高めるための使用材料に関するオプションの特定を強調して、計画段階から始まる。
この点で安全目的の考慮は、ユーザ団体の「趣旨適応」の目的と提携・統合できる。
したがって、設計された製品が安全でかつ効果的に必要な仕事をすることを可能にする。
設計リスクは、設計された製品が変更されるとき、又はそれらの使用環境が変化するときに、存在する。
ライフサイクルのいずれの局面でも採用を決定する者は誰でも安全設計への取組みに専念すべきである。 まさしく設計専門家を超えて設計の機能にかかわる多くのグループがいる。
安全設計は特に以下のグループに関連する:
- 設計専門家(例えば、建築家、技術者、ビル検査者)
- デザイン決定に重要な影響がある他のグループ(例えば、開発者、所有者、事業者、投資家、保険会社、プロジェクト・マネージャ、購入者、顧客及び監視者)
- 供給者(メーカー、輸入業者、プラント賃貸業者を含む)、建設業者、設置者及び取引き/保安要員
- 規制当局、検査監督担当官
図1 − 設計された製品のライフサイクル

より安全な作業場と工場設備を作る機会は、設計された製品のライフサイクルの最も早い段階が最も費用効率がよい。対照的に、設計された製品が輸入、供給又は試運転(ビルの場合)の準備ができている時には、製品を本質的に安全にするオプションは殆どみられない。
傷害、疾病、病気の人的費用に加えて、貧弱な設計は、低い生産性とより高額な維持費・高い雇用、労働者の補償費用の増加、減少する資産耐用年数などのさまざまな経済費用への影響をもたらす。
1.4 作業場における死傷者について設計の役割
労働安全衛生委員会による委託研究は、貧弱な設計がオーストラリアにおける死傷災害の発生に関与しているとみている。この研究は、1997年から2002までの間にオーストラリアの設計関連の作業場における死傷災害の発生を調査した。また、それは貧弱な設計問題の本質及び限界を示した。
研究は以下を示す:
- 210件のうち77件(37%)は、確実に又は多分に設計関連の問題にかかわる作業場における死者と確認された。 別の29件(14%)では、周囲の事情から設計問題の関わりを示唆している。
- 設計は少なくとも30%の仕事関連の重大で致命的な傷害の原因になっている。
- 設計関連の問題が「機械及び固定された工場設備」グループ及び「可動の工場設備、輸送」グループで最も際立っていた。
- 同様の設計上の問題は多くの致命的な災害にかかわった。
- 設計関連の問題は、おおむね採掘、輸送、農業、建設、貿易及び製造業で少なくとも災害の半分にかかわった。
- 特定された設計問題の大部分について解決策は既に存在している。
この研究から重要な発見は、設計がオーストラリアの作業関連の重篤災害の深刻な原因であり続けていることである。これには、機械、生産設備、装置の(かかわり合いの範囲がそれらの間で異なる)さまざまな事例がある。 データ内容の制限は、この分析で特定された設計貢献が過小評価されそうなことを意味する。
1.5 法的な枠組み
オーストラリア安全衛生法は、図2のように、法律、規則、及び実務規範と規格のコードを含む裏づけ資料によって規制されている。 各州・各地区は、中央の法律、主要な労働安全衛生法を有する。 この安全設計指針は勧告である。
図2 − オーストラリア労働安全衛生法令の枠組
1.6 注意義務
オーストラリア労働安全衛生法は、現在、安全衛生に影響を与える可能性を持つさまざまな関係者に義務を課している。 これらは設計者、メーカー、輸入業者、納入業者、設置者及び建設業者を含んでいる。 これらの関係者は、特定の設計された製品に関連して安全衛生を確実にする役割がある。 最も一般的に規制された領域は、工場設備の設計、製造、輸入、供給、設置、建設及び材料の製造、輸入及び供給である。ビジネス又は設計された製品に適用される州及び地区の労働安全衛生法によって、義務は異なる。 安全設計アプローチはシステム・アプローチを提供する。 労働安全衛生リスクの管理にシステム・アプローチを採用することは、関係者が法律上の義務を満たすのを支援する。
1.7 安全設計の遂行
安全設計は、安全について明確に「川下」に影響を与える「上流」の決定に関するものである。現実の危険は作業場にある、しかしながら、原則は、公衆と消費者安全及び普通法と制定法の遂行は両者に、同時に実行されている。 彼らが、普通法と制定法のケーススタディを申し込むとき、設計者、メーカー、納入業者及び輸入業者は注意義務がある。
1.8 安全設計の利益
安全設計アプローチはいくつかの利益をもたらす。 多くの利益が、以下を含んでいる:
- より安全な作業場
- 生産性の向上
- コストの減少
- 安全衛生法に対する、より優れた順応
- 改善
1.9 定義
(Alter)
変更する |
変更が安全衛生に影響する可能性がある場合は、設計を変える、加える又は除去する。但し、日常業務としの維持、修理又は交換は含まない。修正と改装は含む。
|
(Authority)
監督機関 |
連邦、州、地区の労働安全衛生に責任ある監督機関、更にその機関によって派遣された監督機関の職員を含む。
|
(Building or structure)
ビル又は建造物
|
土地の上又は土地に付随する建造物、ビルへの増築、ビルに付属の建造物、ビルの一部。
|
(Construction project)
建設事業
|
建設工事にかかわる事業;準備、設計、計画、顧客の目的達成に必要な建設工事を含む。
|
(Construction work)
建設工事 |
建設、変更、変換、準備、試運転、改造、修理、維持、廃棄、建造物の破壊又は解体に関して行われる建設現場或いはその周辺で行われる作業並びに以下を含む:
(a) 建造物又はその一部の破壊又は解体並びにそれに伴って生ずる副産物又は廃棄物の建設現場からの撤去
(b) 建設現場における建造物のプレハブ部材 (例えば、前もって成形されるコンクリートパネル及び同様のプレハブ部材)、製造又は建設、販売用の在庫は含まない
(c) 建造物を形成するプレハブ部材の組み立て又は分解
(d) この定義で言及した作業目的を達成する掘削、造園、準備工事、敷地造成に関する工事
(e) この定義で言及した浮標、航行への障害、いかだ、船及び難破船を含む水面下の作業、ただし探査又は抽出が行われる場所で行われる鉱物資源の探査、抽出又は準備工事は含まない。
|
(Commission)
作動させる
|
作動させる、稼動する。
|
(Competent person)
有資格者
|
所要の仕事を遂行するために必要な訓練、資格、経験又はそれらを組み合わせた知識・技能を有する者。
|
(Concept development)
概念開発
|
設計の初期機能。それは(どのように設計された製品が職場で必要か)機能的な仕様を提供する。 更に必要な多くの選択肢や取組みを含む場合がある。 |
(Construct)
建設
|
組み立て、構築、変更及び改修。 |
(Design)
設計
|
個人及びグループの芸術的、更に産業の要件を満たす工芸品、製品、プロセス又はシステムを計画し、創出する革新、美意識、及び機能性を纏めるのに使用する概念。 それは研究開発、概念設計、一般的な設計、図面、計画、システム、量、工法又は製法、詳細な費用と危険分析(労働安全衛生リスクの分析を含む)、実行可能性、詳細な設計、技術仕様書及び再設計を含む。
|
(Design phase)
設計段階
|
下流のユーザと協議して設計の選択肢及びトライアルの開発にかかわる。 |
(Designed-product)
設計された製品
|
設計されるべき項目:建設の環境、設備、化学材料、作業システム又はプロセスがある。 更に、他の物理的な属性又は作業場所又は人々との整合性のいずれかに関連づけたシステム。
|
(Design verifier)
設計検証者
|
工場の細目の設計と関連して、工場設計の検証に責任のある有資格者を意味する(その有資格者は、工場設計者と同一人物に雇用されないか契約されない)、工場の細目設計を請け負うために品質システムを使用し、そのシステムがオーストラリア及びニュージーランド(JAS-ANZ)の共同認可制度によって承認又は公認された場合を除く。
|
(Documentation)
文書化 |
法律の規定に関連して、義務履行者が一般的な義務、履行方法又は計画的な過程に適合する手段を文書化するように要求する規定を意味する。
|
(Downstream/ Upstream)
川上・川下
|
ライフ・サイクルに沿う各段階を示すために使用される用語―「川上」危険性除去の最高の効果を達成できる設計の開始段階(概念・設計段階)―「川下」危険性除去の効果を変えるのがより困難な使用・維持段階
|
(Erect)
建設する
|
建造物又は工場の建造物を組み立てる、解体する又は変更する。 |
(Fault)
欠点
|
安全衛生に更に危険をもたらす恐れのある欠陥 |
(General duty)
一般的義務
|
(理念として)立法に関連して、結果か、又はとるべき措置かを特定しない明白な陳述(特に一般的な条項を除く)。取組みにおいて合理的に実用的である限り、義務履行者が注意を喚起するように要求する。
|
(Hierarchy of control)
制御の階層
|
傷害か疾病、器物破損、環境或いはこれらの組み合わせに関する危害の潜在性の原因又は状態。 |
(Hazard identification)
ハザードの識別
|
傷害、疾病又は損害の潜在的原因を識別する過程。 異なった方法は、ハザードを確認するのに使用可能、以下を含む:観察;労働者、顧客又は他のユーザとの協議; モデル又は原型のトライアル; 技術規格及び他の情報源の評価; モニター及び測定。
|
(Hierarchy of control)
制御の階層
|
リスクの排除またはリスクを最小限にするのに使用可能な優先順の制御手段一覧表。 危険を排除できるか否か、制御の階層の適用は、まず第一に評価することが必要である。 これが(合理的)実用的でない場合は、代替が考えられる。 代替が(合理的)実用的でなければ、順番に設備の隔離、工学的管理、管理手順及び個人用防護服・保護具の使用など実用的な考慮を払う。一つの制御措置から制御措置の組み合わせが危険の減少をコントロールするまで適用され、この階層構造は許容可能水準にいたるまで適合される。
|
(Import/ Importation)
導入する・導入
|
国内において或いは国外の別の管轄権から、管轄権を持ち込む。 |
(Install)
設置する
|
所定の位置に取り付ける及びサービス又は使用のために設定する。 |
(Lifecycle)
ライフサイクル
|
設計された製品の寿命のすべての段階。 特定の段階は、製品のタイプに依存しているが、以下を含むと考えられる:設計、開発、製造、工事、組み立て、輸入、供給、分配、販売、賃貸、リース、格納、輸送、設置、建設、試運転、使用又は操作、消費、維持、修理、清掃、調整、点検、修理、変更、改装、改新、再生、転売、廃止、解体、破壊、中止、処分。
|
(Maintain)
維持する
|
良好な状態及び稼動を維持する。 |
(Manufacture)
生産する
|
生産する、 組み立てを含む。 |
(Modify)
変更する
|
変更する(上記の定義alterを参照)。 |
(National Standard)
国家規格
|
労働安全衛生委員会はオーストラリア全域にわたる多くの産業と作業場に共通の危険に対して労働安全衛生規格を設定する。 それらの規格が各州、各地区の規則として採用されるまで、これらの規格は法制化されない。
|
(NOHSC)労働安全衛生委員会 |
オーストラリアの国家機関、当機関はオーストラリアの作業場における死亡、傷害、疾病を予防するための国家的活動を先導し調整する。
|
(NOHSC members)
労働安全衛生委員会メンバー |
労働安全衛生委員会は議長を含む18人のメンバーで構成する;労働安全衛生委員会事務局の最高執行官及びオーストラリア人、州・地区政府、オーストラリア労働組合協議会(ACTU)を介する労働者;オーストラリア商工会議所(ACCI)を介する使用者。
|
(Plant)
工場設備
|
機械、設備(足場を含む)、装置、器具、道具、部品、取り付け部品、付属品。
|
(Procure)
調達する
|
組織のために必需品を入手する。購買にかかわらず、交換、リース、賃貸、分割払い又は契約。設計された製品の設計及び又は製造のための必要条件を指定する契約を含む。
|
(Redesign)
再設計する
|
再度又は異なった設計をする。 或いは、新たな設計。 |
(Refurbish)
改装する
|
変更する(上記の定義alterを参照)、回復する、変更又はアップグレードする。 |
(Repair)
修理する
|
作動状態を元に戻す、但し通常の保守、交換又は変更を含まない。 |
(Residual risk)
残留リスク
|
制御、障壁、その他のリスク低減方法・技術の適用後にも残る危険。 |
(Restore)
復元する
|
原状に戻す又は修理調整する。 |
(Retrofit)
改良する
|
製造後の変化及び開発を取り入れるために製品に修正を加える。 |
(Risk)
リスク
|
ハザードに関して、ハザードへの暴露から起こる負傷、疾病又は損害の発生確率及び結果を意味する。
|
(Risk assessment)
リスクアセスメント
|
特定されたハザードへの暴露から起こる負傷、疾病又は損害の確率と発生結果を分析するプロセス
|
|
設計の検証を必要とするハイ・リスク工場の明確なリスト。(例えば、工場用の国家規格の場合) |
(Scheduled plant)
指定工場
|
(Specification)
仕様
|
義務履行者に取るべき手段を正確に告げ、使用すべき安全装置の特定タイプに付いて述べる規範的な基準(例えば、特定の寸法、形状、色彩の非常停止ボタン用の要件)。
|
(Structure)
建造物
|
(上記の定義buildingを参照)
|
(Substance)
資材
|
固体、液体、ガス、蒸気の形態に関係なく、自然又は人工の材料。化学的実体、複合材料、混合物又は製剤を含み、商品は含まない。
|
(Supply)
供給
|
小売、卸売り、交換、中古販売、オークション、リース、賃貸、分割払い購入及び配給など、再供給のどの形態も含む。
|
(Supply/install Phase)
供給・設置段階
|
供給・設置段階は、安全な受理、格納、出荷及び商取引として設計された製品のユーザへの運搬を含む。 |
(Systematic process)
計画的な過程
|
安全の追求(例えば、危険識別、リスクアセスメント及びコントロール)で続けられる特定の過程又は一連のステップ。 |
(Systems of Work)
作業システム
|
作業過程、作業習慣及び作業方法。 |
(Testing)
試験
|
設計された製品に関連して、製品の試験又は評価の形式を意味する。科学的叉は技術的な査定及びユーザ試験、実験を含む場合がある。 |
(Upstream/ Downstream)
上流・
|
ライフ・サイクルに沿う各段階を示すために使用される用語―「上流」危険性除去の最高の効果を達成できる設計の開始段階―「下流」危険性除去の効果を変えるのがより困難な使用・維持段階
|
(Users)
ユーザ
|
ユーザは、設計された製品のライフ・サイクル中にその製品と接する如何なる人でもありうる。「使用」という用語もライフ・サイクルの「使用又は稼動」の局面で一般的である
|
(Work with)
連携する
|
製造する、組み立てる; 使用する、扱う、操作する; 格納する、輸送する; 設置する、建設する、修理する、整備する、掃除する; その他、作業で遭遇する事項。 |
|
|
|
|
2. 安全設計の原則
2.1 原則―管理又は影響力を持つ人々
管理と責任との直接の関係は安全設計アプローチに不可欠である。安全設計への責任は、安全設計への管理又は影響力を持つ関係者か人々にある。 責任は、人が安全設計の効用上持っている管理の程度と一致する。
設計された製品の仕様に関して管理又は影響力を伴う関係者は次の通りで彼等に限定されない:
- 設計者
- 顧客又は仲介人
- 資本家
- メーカー
- 納入業者
- 賃貸借契約又は賃貸代理業者
- 購入者
- 設置者
- ユーザ
- 保険会社
- 輸入業者
- 建設業者
- 保守管理者
- 同上従業員
2.2 原則―設計された製品のライフサイクル
ライフサイクルアプローチの活用は、製品及び作業システムの安全設計への鍵である。
設計された製品のライフサイクルにおける(図3参照)安全設計は、(設計、製造・工事の方法及び又は製品の安全性を高める使用材料に関するオプションの確認を強調した)概念的な開発段階から始まる。 設計された製品の異なった領域の状況では、これは、作業環境、設備、材料及び又はシステムにおけるハザードへのユーザの暴露又は対人関係の考慮を含む。
本質的により安全に設計された製品を創る機会は、設計、製造又は工事の最も初期のライフサイクルの段階ではより大きい。 これらの初期段階には、ハザードを設計から外す及び又は製品に関する機能条件及び当初の設計概念と互換性があるリスク・コントロール手段の組み込みによって、より大きな領域がある。これらの段階でリスクを除去するか、又は事実上制御できれば、死傷災害は、川下で製品を使用するか、又は働いている人のために回避できる。
各人(最も早いライフサイクル段階で決定を制御するか、又は影響を及ぼす)がこれらの領域におけるハザードに積極的に手を打つ場合は、作業環境、設備、材料及び又はシステムを機能強化できる。
図3 − 設計された製品のライフサイクルにおける安全設計
設計された製品のライフサイクルにおける、それぞれの段階は以下のセクションで説明される。
2.2.1 概念開発段階
概念開発は設計の初期の機能である。 それは、機能的な仕様(設計された製品が何であるかということが作業場に必要である)を提供して、必要なものを送るための多くのオプションかアプローチを含む。 概念開発段階は必要とされる設計された製品の機能ニーズ分析で始まる。 設計された製品の必要な機能に加え、ライフサイクルのすべての段階に関連する安全要件は、機能的な仕様に特定され、含まれる。作業場及び又は作業を管理する人々がしばしば概念開発段階のこの要素にかかわる。彼らが作業場における必要性及び問題を確認するからである。
機能的な仕様は、類似の設計された製品のために問題に関する認識状況の研究で裏づけられる。 そのような類似の設計された製品へのリスクアセスメントの利用と評価は、注意を要する問題に有用な知見を提供する。
また、現存し潜在的なハザードによって影響を受けるユーザの視点を求めるのも必要である。 従業員と連携するためのチャンネルを確立したとき、使用者にとって、協議とフィードバックは一般的にはるかに容易である。 他方では設計者、メーカー及び納入業者は、現存し潜在的なハザードを特定するために有効な繰り返しの協議メカニズムを確立する必要がある(セクション2.5.1を参照)。
設計者及びメーカーは、技術的な市場調査をする間、彼らの提案した設計された製品の潜在的ユーザと協議する。同類の設計された製品の納入業者、輸入業者、設置者及びユーザに付いても同様である。
研究と協議で特定されたすべての問題が、照合され、登録される。 特に設計段階において、それらがライフサイクルの将来の段階を知らせるための使用を確実にする。
事業者・購入者は、購入した設計された製品の労働安全衛生リスクを最小化するように作用する契約の協定と調達システムを持つ必要がある。 そのような手配は以下を確実にする:
- 購入及び契約の協定(例えば、仕様、事前資格審査及び入札文書)は、労働安全衛生のハザードを除去して、リスクを最小にし、更に残留リスクの情報を提供する要件を含む。
- 設計要約又は仕様草稿は、安全設計アプローチを行う書面による協定を含んでいる。 また、協定はライフサイクルの労働安全衛生リスク評価と残留リスク登録の提出を含む。
2.2.2 設計段階
設計段階は川下のユーザとの協議における設計オプション、評価プラン及びトライアルの開発にかかわる。 それは設計プランの一部として以下を含む:
- 設計段階を超えたそれぞれの段階における、リスクの査定
- トライアルと評価プランの開発
- リスク・コントロールオプションの開発
- 安全な工事・製造、供給・設置、稼動・使用、維持、廃棄及び処分・再生のための適切な指示
この時点で設計された製品を作動させる人との協議は、設計者の要件への理解を知らせ、設計からハザードの除外をより有効にする。
設計された製品は、それらを安全に使用できるように設計される。 それは作業場所において働く人々の最大可能範囲の容量に合うように設計することが望ましい。 設計者は、莫大な範囲のユーザの物理的なサイズ、例えば、背の高さ、手の届く範囲、を意識する必要がある。 また、設計者は、労働力の多様性を考慮に入れる必要がある。
設計された製品は、すべての合理的に予見できる用途及びユーザに与える悪影響について評価される。 設計された製品について有効なトライアル及び評価並びにユーザとの協議におけるどのようなリスク・コントロールオプションも設計段階で重要である。 設計のトライアル及び評価は、ライフサイクルのすべての段階に広がる。次のために:
- 設計リスクを観察する
- リスク・コントロールの有効性を確認する
- 必要なコントロール調整をする
2.2.3 工事・製造段階
設計プランに従って、工事・製造段階はメーカー・建設業者にかかわる。 設計プランは、設計された製品に含まれる安全要求事項・特徴と同様に安全な工事・製造のための過程を詳しく述べる。
設計プランに連携するリスク・コントロールのモニター及び評価は、安全な生産過程を確実にするためにメーカー・建設業者のリスクアセスメント及び労働安全衛生マネージメントシステムを要因とする。 トライアルは供給又は稼動・使用に供する前に設計された製品のリスク・コントロールの有効性を確認する。
2.2.4 供給・設定段階
供給・設定段階は、商取引としてユーザに設計された製品の安全な受領、格納、取り扱い及び転送を伴う。
リスクを意識して、ユーザ(使用者、労働者及び又は安全衛生代表)に設計された製品の安全な使用に必要な残留リスクとリスク・コントロールの手段を伝えることは納入業者・設置者にとって必要である。
また、納入業者は、設計された製品の安全な受領、格納及び取り扱いのためにリスクアセスメントを行う。 リスクアセスメントは、設計された製品がオーストラリア国内又は海外に関係なく、設計者及びメーカーによって伝えられた残留リスク及びリスク・コントロールで知らされる。
設計者、メーカー・建設業者及び納入業者とユーザ相互間の協議は、設計された製品が輸入され又は購入された既製品の場合でも、リスクの効果的な除去又は制御において有用である。
納入業者は、作業場をコントロールする人々及び又は作業をコントロールする人々に、商業的に利用可能な設計された製品に関連の安全衛生問題について話し合いを奨励する。 納入業者は設計者及びメーカー・建設業者に関連リスク情報を戻す必要がある。
また、輸入業者、賃貸借契約、賃貸エージェント、競売人又は中古ディーラーは、上記と同様の責任を負う。
2.2.5 稼動・使用段階
ライフサイクルの稼動・使用段階は、設計された製品の作業場への実現を伴う。 それは以下を必要とする:
- トライアル結果及び進行中の評価活動の確認
- 情報の有効な経過
- 適切なトレーニング、指示、及び管理
作業場及び作業をコントロールする人々は、設計者、メーカー及び納入業者からもたらされる残留リスクに関する知識により設計された製品の実現及び使用中のリスクの評価を求める。
この段階で特定された追加設計問題は、メーカー、納入業者及び又は輸入業者を通して設計者に戻す必要がある。
2.2.6 維持、廃止、処分・再生段階
また、それぞれの段階は、リスクアセスメント、残留リスクに関して設計者からライフサイクルを通して情報の利用及びリスク・コントロールの対策を必要とする。また、これらの段階で特定された追加設計問題は設計者に戻す必要がある。
維持段階における設計された製品へのいかなる変更も概念及び設計段階での細目にわたる過程の再適用を必要とする。 これは、新しい危険が導入されないばかりでなく、既に設計された安全性能も影響を受けない及び特定されたリスクの除去・コントロールを改善するための他の機会を確実にする。
2.3 原則―組織的危険管理
設計された製品の設計者、メーカー・建設業者又は納入業者の基本的な義務は、ライフサイクル中に設計された製品の使用又は製品への暴露から危害のリスクを生み出す恐れのあるハザードを除去することである。 ハザードを除去するのが実用的でないならば、設計者、メーカー・請負人又は納入業者はリスクを制御する必要がある。
義務は人が設計、製造・工事又は供給への管理及び又は影響力の範囲で適用される。危害のリスクを管理し及び又は左右する能力は、取り掛かる具体的な機能に応じて異なる。
組織的危険管理アプローチを取り込むことは、関係者がこれらの義務を果たすことを可能にする。
2.3.1 ライフサイクル段階の期間にリスク分析の適用
設計された製品の様々なライフサイクルにおける段階に適切な危険分析の明確な目標については、以下に記載する:
・ 関連するリスクの重大な誘因及び顕著な要因を特定すること
・ 設計過程への入力提供及び総合的な設計の妥当性を評価すること
・ 設計への可能な安全対策を特定及び評価すること
・ 提案された潜在的に危険な施設、活動又はシステムの受容性の評価のために入力を提供すること
・ 定常及び非常事態のための手順開発支援に情報を提供すること
・ 規定及びその他の要件に関してリスクを評価すること
・ 代替設計概念を評価すること
- 製造・工事、供給・設置、稼動・使用及び維持段階:
・ 関連要件との実績を比較するため経験を観察し、評価すること
・ 通常の作動、維持・点検及び非常時対策の最適化に入力を提供すること
・ 危険にさらす大きな誘因及び影響要因に係る情報をアップデートすること
・ 操作上の意志決定のためにリスクの重要性に関する情報を提供すること
・ 組織機構、操作慣行・手順及びシステム構成要素の変動効果を評価すること
・ トレーニングの取組みに焦点を合わせること
- 廃棄及び処分段階:
・ システム処分活動に関連するリスクを評価すること及び関連必要条件を満たすことを確認すること
・ 処分手順への入力を提供すること
2.3.2 リスクの分析処理
設計者、メーカー・建設業者及び納入業者が、それぞれの義務を達成するには以下のことが必要である:
- 設計関連のハザードを特定する
- リスクアセスメントを行う
- ハザードを除去し、リスクをコントロールする
- リスク・コントロール対策を監視し、再検討する
- リスクアセスメントに関する記録を整備する
- 手動の取り扱いリスクに関してユーザと協議する
- ライフサイクル段階の推移とともに、設計された製品の意図する使用に係る情報を提供する。
2.3.2.1 ハザードを特定
ハザードは危害を引き起こす可能性がある。 設計された製品に関連しているハザードに2つの明白な起点がある:
- 設計された製品自体に関連するハザード。 設計された製品は、特定の必要とするさまざまなハザードを持っている。 例えば、医療施設の患者用トロリーは移動性、可動部及びその負荷運搬容量に関連するハザードを伴う、しかし一方、ビル又は建造物には、入り口及び出口に関連するハザードがある。
- 使用方法及び使用環境に関連するハザード。 例えば、患者用トロリーには、ユーザに影響する恐れがある使用表面の勾配及びタイプ(例えば、不安定又は滑りやすいフローリング)並びに動力(負荷の種類)から生じるハザードが考えられる。 設計者は使用項目の環境によってもたらされるハザードを考慮する必要がある。
ハザードの識別は、できるだけ早く概念開発と設計段階で行われる必要がある。それは、設計された製品が完成するか、組み立てられるか及び又は設置される前である。 ハザード識別活動が系統的で1人又は2人の立場の経験に限られていないことは、重要である。
ハザードの系統的な識別は以下を必要とする:
- 研究―類似の設計された製品のユーザ、その他納入業者、メーカー及び又は設計者によって保存されていた傷害及び事故データから研究の記録及び。関係者によって以前に行われたトライアルまで、各種の情報は、設計された製品のハザードを特定し、リスクを評価して、制御するのを助ける。
- 協議―協議はそれぞれのリスクアセスメントの過程のステップと同様に安全設計のすべてのステップで重大な要素である。設計者はハザードに関して設計された製品のライフサイクルにかかわるすべての関係者と協議すれば最善の情報が得られる。
- 指針構成要素―ハザード識別用チェックリストは、精査によって見出され、又は形成される:
- 関係規格
- 実務規範
- 注文書
- 技術標準規格
- 他の情報源材料
- 適切なシステム及びツール― リスク管理システム及びリスクアセスメントツールは、設計された製品領域(それは、ビル、工場設備、材料または作業システムか?)及びリスクタイプ(人力操作、閉塞空間、墜落・転落又は他のリスクか?)に見合う必要がある。
- リスク管理システム― 設計者は、評価するためリスクの範囲を裏付けるリスクの状況を見極め、適切なリスク管理システム及びツールが適所にあるのを確実にする必要がある。 リスク状況は、潜在的に発生する危害及び又は費用効果に関して活動(例えば、高層工事、国内のビル、高圧設備及び重機揚荷設備は、すべて非常に異なった状況下にある)の複雑さと本質及び結果のレベルに関連する。リスク管理システムは、一般に、次を包括する:
- 割り当てられた役割及び責任(誰がリスクアセスメントを行い、是認するか、及び誰がリスクをモニターし伝えるかを含む)
- 指針はリスクの許容レベルに関して提供。
- 貿易・専門家及びリスク管理トレーニングが必要 (作業場に存在するリスクの範囲をリスク評価するために有用な技能)。
- 要件及びメカニズムが確立した協議・伝達(リスクの識別、評価、コントロール及び又は継続的モニターに係わるリスクで影響を受ける関係者はどうか?現段階後のリスクについて誰がどのように知るか?);
- リスクのモニター、レビュー及び連続的改良過程(どんなトライアル又は評価が行われるか、更に、それらの有効性をリスク・コントロールによってどのようにチェックされるか?)
- 使用されるリスクアセスメントツール
- リスクアセスメントツール及び技術― リスクアセスメントツールはリスクの状況によって、選択される。 使用されるリスクアセスメントツールの例は:
- HAZOP(ハザード実現性研究)―ハザード及び実現可能性の問題を特定するための手法。それは特定の過程が予想された操作から逸脱するすべての方法の重要性をグループレビューするのに使用する。 テクニックは、工事前に詳細な設計レベルで処理設備の各部分を調べるのに特定の見出語を使用する構造化されたブレーンストーミングアプローチである。 それは処理工場設備において特に適切であるが、設計の他の製品領域に適用するために異なった見出語の使用で変更することができる
- ETA(事象のツリー解析)―起因事象及びそれらの頻度を可能な結果に特定するのに使用される。
- FTA(欠陥関連樹解析法)―望まれない事象を導く条件及び要因(又は、頂上事象)を特定(絵入りで表現)するのに使用される。機能的なシステム(又は、製品の要素)の考えられる原因又は欠点モードは、「何が間違いの可能性があるか?」を評価することによって、特定される。
- FMEA(故障モード影響解析)―構造的又は機械的な設計における起こりうる失敗を特定するのに使用される。 その過程は、調査が潜在的モード、失敗の結果及びこれが全体として要素及びシステム上有する効果を特定するように、設計を適正水準に分析する。
- PHA(予備のハザード分析)―与えられた活動、施設又はシステムのために危害を引き起こす場合のハザード、危険な状況及び出来事を特定するのに使用される。プロジェクトの開発の初期に一般的に使用する。しかし、この方法は、より大規模な方法を使用できない場合には、既存のシステムを分析するか、又はハザードを最優先させる場合に使用できる。
- HRA(人間の信頼性評価)―信頼性への人為ミスのシステム性能と影響を取扱う。
- CHAIR(工事ハザード評価)―工事の安全設計のために特に設計された系統的なツールを提供する(詳細はPart 4)。
- その他のツール、追加手法の詳細はオーストラリア及びニュージーランド標準規格3931(1998)「技術システムのリスク分析―適用案内」に提供、以下を含む:
- カテゴリ格付け
- チェックリスト
- 共通モード故障分析
- 結果モデル
- デルファイ法
- ハザードインデックス
- モンテカルロシミュレーション及びその他のシミュレーション手法
- 一対比較
- 史料レビ
- スニーク分析
状況が何であっても、設計された製品領域が管理されていればどれでも、リスク評価システム又はツールが使用されていれば何でも、プロセスは概して同じまま残る。 リスク管理プロセスは図4に示される。
図4 − リスク管理プロセス
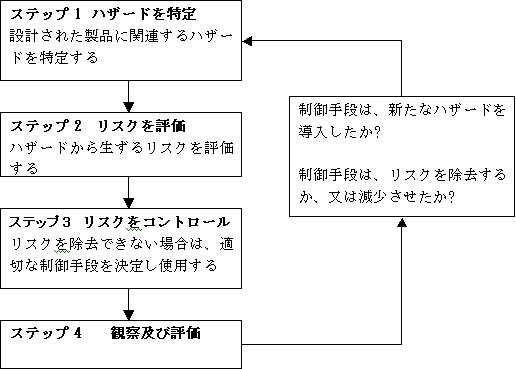
2.3.2.2 設計された製品の危害のリスクを評価
設計された製品のライフサイクルのどの段階でも使用にすることが危害をもたらす可能性があれば、設計者、メーカー・建設業者及び又は納入業者は、リスクを分析し、評価する必要がある。 分析は決定するため研究を活用する:
- 既存の制御がある場合
- 有害事象の発生見込み
- 有害事象の結果
- リスクに伴う推定レベル
評価は、リスクの許容可能な水準で提供された指針に対しておよそのリスク水準との比較を考慮する。 また、それは除去又は制御の次のリスク管理ステップに至るリスクの優先順位づけに備える。
2.3.2.3 除去又はそれが実用的でない場合はリスクを制御
設計された製品の評価が容認できないレベルのリスクをもたらす場合は、設計者は、製品の再設計局面でリスクを設計から除外できるか否か考慮する必要がある。 しかしながら、設計リスクが極端であるか非常に高く評価されるならば、設計手法は、再考の必要がある。 基本的に異なった設計手法が、それらのリスク除去に必要なことがある。
リスクを除去することができない場合は、設計者は、実用的である限り1つ以上の制御方法を使用してリスクを最小化することを試みる必要がある。
制御の階層(下記セクション2.3.2.4で詳述)は、最も効果的なリスク・制御オプションの検証促進に使用される。
設計者は、適所に置かれた制御もユーザのために別のリスクを生じないか又は新たなハザードを導入しないかを確認する必要がある。
リスクの除去又は制御を試みた後に残留リスクが異常に高く残っている場合は、設計者は、残留リスクの情報を提供し、作業場において制御に必要な対策について助言する必要がある。 設計された製品のメーカー、納入業者及びユーザにすべての関連情報を提供する必要がある。
2.3.2.4 制御の階層の使用
制御の階層モデルは、リスクアセスメントプロセスの制御段階で使用のため問題解決及び創造的思考ツールとして通常、提示される。 それは、オプション識別を制御するために優先順位のアプローチを提供する。 基本的に、制御の階層は以下を必要とする:
- 最優先としてのハザードの除去
- ハザードを除去出来ない場合は、以下によるリスクの最小化
- より安全なものに置換する。
- 工場設備又は作業システムを変更する
- 工場設備又はシステムの危険な局面を隔離する
- 工学的制御を導入する
- バックアップ'制御の導入、以下による:
- 運営管理制御及び安全作業訓練を実行する
- 個人用保護具の使用を必要とする。
階層構造の上位のリスク制御は、労働者による入力の必要なしに機能し、一般的に受身の安全対策と呼ばれ、より効果的である。可能である場合はいつも、受身の安全対策の使用は制御手段として好まれる。 例えば:
- 機械装置の防護
- セーフティ・インターロックシステム
- 漏電デバイス(また、残留電流装置として知られる)
受身の安全対策として、事故発生(例えば、機械装置の防護)の頻度を減少、及び事故(例えば、工事用機器の転倒防止構造; 残留電流装置)に起因する傷害の頻度又は強度の減少、又は、傷害の重大さの減少さえも(例えば、安全アラームシステムは、早期の局所化と負傷者の処理を考慮する)設計可能である。
これらは、労働者の行動又は協力を必要としないで、不測の事故が起こるか又は労働者か他の者が設備の意図通りの使用とは無関係の機能なので、好まれる。
殆どの受身の安全対策は、設備、ビル又は仕事のシステムに設計され、機能している。このため近年、労働安全衛生への設計の貢献に関心が集中している。
2.3.2.5 残留リスク及びリスク制御対策の有効性のモニター及び評価
設計者、メーカー及び納入業者は、それぞれ適用したリスク制御対策の有効性をモニター及び評価する義務がある。 設計者は、最初に設計された製品及び作業システムトライアルでリスク制御の有効性を確認する必要がある。 これは特定された範囲の仕事及び用途の全域で制御原型研究を含む可能性がある。 そして、設計者は、製品及び作業システムがライフサイクル段階を通して推移する場合には、リスク制御の進行中の評価及び是正・修正を確実にする必要がある。
メーカーと納入業者は、内部的に特定されて、実行されたものと同様に、設計者によって伝えられたリスク制御を、観察し評価する必要がある。新情報及びより効果的なリスク制御は、設計者に戻されるのと同様にユーザーに伝える必要がある。また、彼らは、改良されたリスク制御を知らせる新情報をモニターして、すべての関係者に確実に伝える必要がある。(セクション2.5.1の図7を参照)
2.3.2.6 リスクアセスメントに関する記録の維持
設計者は、特定したリスクに関する記録を設計過程及びそれらのリスクを除去するか、又は最小化するように取られた段階の間、保持する必要がある。設計者は、作業場で使用中の設計された製品の残存期間と同程度の間記録を保存する必要がある。
さらに、新情報が利用可能になって、設計がこの情報を考慮して変更される場合には、この記録は保存する必要がある。
メーカー、納入業者及びユーザにリスクを伝える最も効果的な方法は、設計者が、リスクアセスメントを彼らに利用可能にすることに、気づくことである。 これは人々と作業環境が1つの作業場から別のところに明らかに変わるとき、メーカー、納入業者及びユーザがそれら自身のリスクアセスメントを行う必要性を必ずしも排除するものではない。
2.4 原則―安全設計のための知識及び能力
安全設計に対して管理及び影響力を持つ設計者や個人によって立証され又は利用可能な技能及び知識は、以下を含む:
- 労働安全衛生規則に関する知識
- 調達における労働安全衛生に関する知識
- ハザードの識別及び分析
- リスク評価及びリスク制御
- 人間の挙動に関するデータを調達、確認、分析する能力
- さまざまな情報源及び専門分野からの知識を新しい解決策に統合する能力
- 協議、交渉及び影響力の技能
- 立案方法
多くのシステムが1人の人に十分に理解できないくらい複雑であり、多くの人材が、かかわり・協議されるべきである17、以下の人々を含む:
- 設計された製品領域に関する十分な知識
- 他の専門知識、例えば、リスクアセスメントを行うのに必要な知識
安全設計に関する助言のための能力指定の1例は、職業教育・訓練制度で開発された能力に関する「高度資格レベル業務訓練パッケージ・ユニット」である。 能力に関するこの単位は、製品のライフサイクルの間、労働安全衛生リスク制御に安全設計原則の適用について助言する労働安全衛生実務者に必要な知識及び技能の範囲を指定する。 これは経営される特定の産業及び製品の事情で適用される包括的な単位である。
安全設計の技能及び知識への国際的な産業特有のアプローチに関する例は、「セクション3.5 原則―知識及び能力」で概説される。
質問1: 安全設計の1連の中核となる能力又は技能は、重要なリスク又は広範囲に影響のプロジェクトに関係する人々の義務と考えるべきか? これらは、どうあるべきか? これらの能力は、各製品ごとに特定されるべきか、それらは、一般的でると共に各状況ごとに当てはめることができるか? |
2.5 原則―主要情報の転送及びフィードバック
情報提供は、製品に関連する人々がかかわったリスク、リスク制御対策及び特定の訓練要件も意識する過程である。 リスク制御に必要な動作に関して、ライフサイクルの後期で主要な情報を設計段階からすべてのユーザまで適切に記録すると共に転送する必要がある。そして、ユーザは、それらを制御するためにこの安全衛生とメカニズムに恐らく影響する残留リスクに関しても知らされる必要がある。 すべての関係者が新たに特定されたか、又は自覚したリスクに関して同様に上流の関係者にフィードバックを保証する必要がある。 図5は情報の相互的な転送及び安全設計のアプローチに必要なフィードバックについて表す。
図5 − フィードバックによるライフサイクル
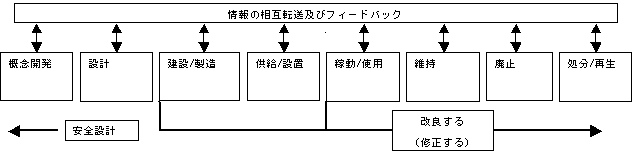
理想的に良い設計は情報の必要性を削除する必要がある。 製品、システム、設備、ビルなどは、取扱説明書なしで安全かつ容易に使用する必要がある。 しかしながら、ラベル、取扱説明書、消極的な警告などは設計によって軽減出来ないハザードに対処する手段である。
そこでは、設計の選択を介してハザードを除去すること又は特別な手順及びトレーニングを取り入れ安全警報装置で関連リスクを許容レベルまで引き下げることは非現実的である。18
また、取扱説明書、警告、ラベルなどは良い設計を必要とする。これらの有益な機能の追加は、注意深い考慮なしではできない。 つまり設計者は、より信頼できる手段で理想的に記述されたハザードを軽減するこれらの手段に期待している。
…手順の使用が安全を達成する唯一の実用的方法であるならば、誤りの機会が高く、最高の明快さが必要だと認知しなければならない。
リスク制御として有効な情報を設計するのは、大変困難である。 設計者が、情報を提供することが唯一のリスク制御オプションと考えるならば、設計者は、情報の必要性が設計から除外できるかどうか確認するために設計を再考する必要がある。 図6は情報最小化の段階を進める繰り返しの情報設計ループを提供する。
図6 − 情報設計ループ
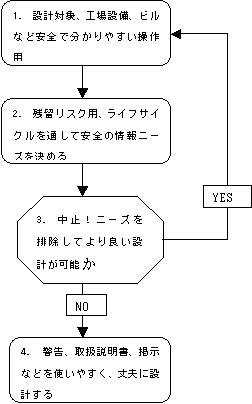
情報規定の細目は、設計された製品のタイプに従って異なるが、次を含む:
- 建設、設置、試運転又は始動に関与
- 輸送又は格納に関与
- (いったん生産された場合)エンドユーザとして使用、操作、その他の作業にかかわる者
- 進行中の清掃、維持、修理又は調整に関与
- 失敗、故障又は閉塞に対応
情報規定の異なった書式は、製品安全データシート又はマニュアル、ラベル、安全衛生ファイルを含む。 材料のための製品安全情報はよく整備されている。 承認されたメカニズムは、ラベル及び材料安全データシートであり、それぞれに国の実務モデルコードがある (即ち、作業場における材料の表示用実務コード:労働安全衛生委員会、1994)。
工場設備のために、メーカーが工場設備に添付する警告ラベル・掲示及び又は操作マニュアルを作成するのは、一般的な習慣である(労働安全衛生情報を含む)。 この情報の範囲と品質は変えられる。 オーストラリアの労働安全衛生法令のすべてが、工場設備のメーカー、輸入業者及び納入業者に情報を提供するように要求している(殆どの州及び地区が設計者に同様の義務を規定する)。
2.5.1 協議
工場設備、作業場レイアウト、作業システムなどに関する設計決定によって潜在的に影響を伴う作業場内において協議する方法は、現在一般的である。 作業場の中のこの要素の安全設計への責任を伴う使用者は、影響する協議なしでは義務を履行できない。 しかしながら、図7のごとく設計者と川下の関係者との間の安全設計に関する協議は、現在、影響する意見を求めるため形式的な仕組みなしで存在する。 このように協議することへの障害は全くない。