機械安全とは
機械設備による労働災害(以下、機械災害という)は依然として死傷災害全体の約1/5を占めており、製造業においてはその比率は約4割に増加します。機械災害は、機械のエネルギーが大きいことから、はさまれ・巻き込まれ等により身体部位の切断・挫滅等の重篤な災害や死亡災害につながることが多いのが特徴です。
一方、機械はその使用状況をあらかじめ想定できますので、設計・製造段階でリスクアセスメントを実施し保護方策を織り込んだ機械を使用者に提供し、使用者がさらにリスクアセスメントを実施して機械を安全に使用すれば確実に機械災害の大部分は防止できます。国は「(改正)機械の包括的な安全基準に関する指針」(平成19年7月31日付け基発0731001号、以下「機械包括安全指針」という。)を公表し、機械の安全化を図ってきました。さらに、労働安全衛生規則第24条の13により機械危険情報の通知を努力義務化し、あわせて中災防などの機関により機械安全にかかわる人材育成を推進してきたところです。
1. 機械の安全化の原則
機械の安全化を進める上で、3つの大前提があります。それは、
- 人はミスをする
- 機械は故障する
- 絶対安全は存在しない
の3つです。
人の注意力には限界がありますので、人がミスをしても事故・災害に結びつかないように、「人の注意力に頼る安全」からより信頼性の高い「機械に任せる安全」にすることが効果的であり確実です。しかし、信頼性の高い機械も時には故障することがあることを認めて、故障しても安全機能が継続するように考慮することが必要です。絶対安全に関しては、どんなに安全化を進めても「残留リスク」はゼロにはならないことが、JIS Z 8051(ISO/IEC Guide51)「安全側面―規格への導入指針」に示されていますが、リスクアセスメントにより「受け入れ可能なリスク」のレベルまでリスクを低減することが機械の安全化に求められる基準であり、そのレベルは合理的に実現可能な技術水準とされています。
機械災害を確実に防止するための機械の安全化の原則があります。それは、下記の3つです。
- ①本質安全の原則
機械の危険箇所(危険源)を除去する、又は人に危害を与えない程度にする。例えば、角部を丸くする、作動エネルギーを小さくするなど。
- ②隔離の原則
人が機械の危険源の接近・接触できないようにする。例えば、柵や囲い等のガードを設ける
- ③停止の原則
一般的に機械が止まっていれば危険でなくなるので、人が機械の動作範囲に入る場合は、インターロック等で機械を停止させる、又は停止してから入場を許可する
2. 機械包括安全指針による機械の安全化の手順
図1に機械包括安全指針に基づく機械の安全化の手順を示します。機械の製造等を行う者(メーカーだけではなく、輸入業者やユーザー事業場で製造機械の設計・改造を行う部門が含まれる)は、機械の設計・製造段階でリスクアセスメントを実施し、その結果に基づいて必要な保護方策を適用し、適切にリスクの低減を図ることが求められます。
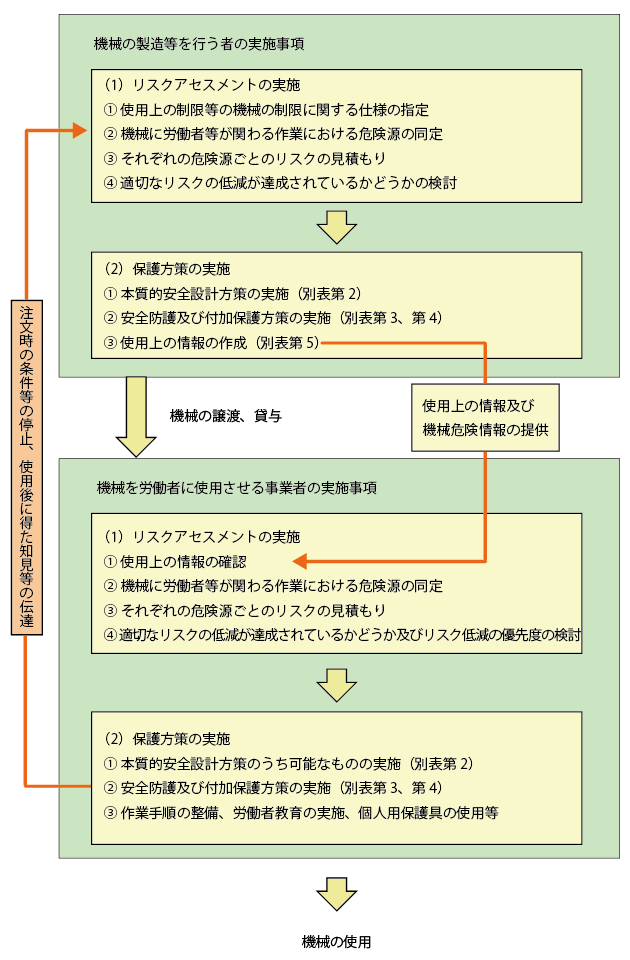
図1 機械包括安全指針に基づく機械の安全化の手順
保護方策実施後の残留リスクについて、「残留リスク一覧」、「残留リスクマップ」、を「機械の制限仕様」と合わせて、ユーザーに機械危険情報として伝達します。
機械を労働者に使用させる事業者(ユーザー)は、メーカーから提供された「使用上の情報」及びそれに含まれる「機械の危険情報」の内容を確認するとともに、実際に機械を設置する環境、使用方法をふまえてリスクアセスメントを実施し、その結果に基づいて必要なリスク低減方策を実施します。保護方策を実施後の残留リスクに対しては、作業手順の整備、教育訓練の実施などの管理的方策や、必要に応じて個人用保護具の使用を行います。「機械の危険情報」はユーザーがリスクアセスメントを実施するために不可欠なものですのでメーカーに提出を求めて下さい。もしメーカーが提出できないようであれば、その機械は「リスクアセスメントが実施されていない危険な機械」とみなされますので購入を見合せることをお勧めします。
ユーザーからの「注文時の条件等の提示」は、メーカーのリスクアセスメントの条件となり機械の安全化に有効です。さらに使用後のユーザーからメーカーへの情報・知見のフィードバックは、今後の安全化に役立ちます。ユーザーからメーカーへの情報提供については、平成26年4月15日付け基安発0415第1号「機械ユーザーから機械メーカー等への災害情報等の提供の促進について」に定められています。
ユーザーにおいて機械を改造する場合は、メーカーと同様にリスクアセスメントを実施し、適切にリスク低減を図る必要があります。また既設の機械についても、リスクアセスメントを実施し、その結果に基づいて適切なリスク低減を実施すれば、機械災害の防止に大きな効果があります。
「機械に関する危険情報の通知」を活用しましょう
3. リスク低減方策について
リスクアセスメントを実施した後のリスク低減方策については、3ステップメソッドと呼ばれる保護方策の優先順位があります。
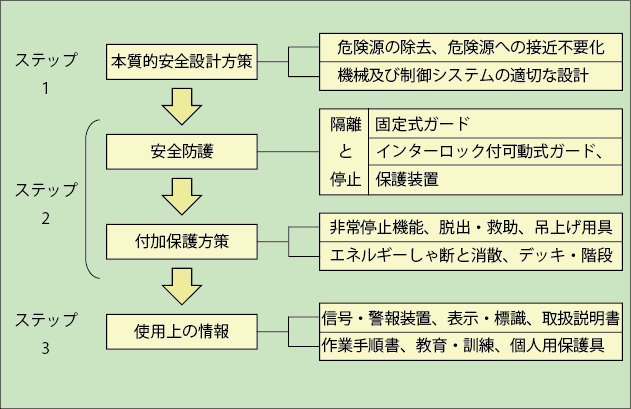
図2 3ステップメソッド
(1)本質的安全設計方策(機械包括安全指針別表第2)
本質的安全設計方策は、「ガード又は保護方策を使用しないで機械の設計又は運転特性を変更することによる保護方策」とされています。つまり
- ①設計上の配慮・工夫により危険源そのものをなくす、又は危険源に起因するリスクを低減する、又は危険源になることを防止する
- ②作業者が危険区域に入る必然性をなくす、又は頻度を低減するに大別されます。次のような例があります。
機構的に危険な部位をなくす
- 人に接触する可能性のある部位から鋭利な端部、角、突出部をなくす
- はさまれるおそれのある部分は、進入できない程度に狭くするか、はさまれない程度に広くする
- 身体に被害が生じない程度に駆動力を小さくする
- 身体に被害が生じない程度にエネルギーを小さくする
- 動力に低電圧を使用する
- 騒音、振動の発生、危険物の飛散、放射線の漏洩を防止する
- 危険物・有害物質を使用しない又は最小限にする
危険源にならないようにする
- 一般的設計技術を活用し、機械が正常に作動するよう配慮する(応力、材料、経年変化等)
- 人間工学的配慮により、身体的負荷、誤操作を低減する
- 機械が危険な挙動(予期しない起動等)をしないように、制御システムを正しく設計する(再起動防止(自己保持回路)、二重化・冗長化、非対称故障モード等)
作業者が危険区域に入る必然性をなくす
- 機械の信頼性を向上し故障を防止する
- 材料の供給・製品の取出しを自動化・遠隔化する
- 保全作業等を危険区域の外からできるようにする(自動監視、遠隔監視、遠隔調整等)
- 給油・給脂作業を外部から実施又は自動化する
(2)安全防護(機械包括安全指針別表第3)
安全防護は、ガード又は保護装置による保護方策で、隔離と停止の原則の応用です。
ガード
- 固定式ガード
恒久的に固定されているか工具を使用して外さないと内部に入れない構造のもの。(囲い又は覆いに相当するもの)
危険源に応じて、高さ、開口部の大きさ(すきま)、危険源との間の距離にJIS規格の規定があります
- 可動式ガード
工具を使用せずに開くことができるもので、固定式ガードに設けられた扉や蓋等です。
開いた場合に危険源に曝露されるので、開いたら停止する、又は停止しないと開かないインターロックが必要です。
保護装置
インターロック装置
- 能動的光電保護装置(AOPD)
一般的にはライトカーテンと呼ばれるもので、投受光器を遮ると機械の運転許可を取り消し、停止させます。
- 拡散反射型能動的光電保護装置(AOPDDR)
一般的には、レーザースキャナと呼ばれるもので、スキャニング範囲に入ったことを検出して機械を停止させます。
- イネーブル装置
ボタン式又はグリップ式のスイッチで、軽く握っている時だけ運転が可能になり、危険な状態で手を離したり握りこんだりした時には機械を停止させることができます。ロボットの教示ペンダント等に使用されます。
- ホールド・ツゥ・ラン制御装置
手動操作装置のスイッチで、押しているときだけ機械が動き、手を離せば機械が停止するものです。
- 両手操作制御装置
作業者が両手で同時に操作したときだけ機械が起動できるもので、プレス機械の起動装置に使用されます。操作者自身の安全が確保できるが、第三者の安全は確保できません。
イネーブル装置、ホールド・ツゥ・ラン制御装置、両手操作制御装置は、安衛則第107条第1項の「覆いを設ける等」の制御モードでの運転操作に使用できます。
(3)付加保護方策(機械包括安全指針別表第4)
付加保護方策は、労働災害に至る緊急事態からの回避等のための保護方策です。ハード対策ですが「人が操作してあるいは正しく使用して有効となる」方策ですので安全防護とは一線を画するものですが、必要不可欠なものばかりです。
付加保護方策
- 非常停止機能(非常停止装置)
- 捕捉された人の脱出及び救助手段
- エネルギーの遮断及び消散の手段
- 機械及び重量物の運搬・取扱手段
- 機械類への安全な接近手段(階段・デッキ・手すり等)
(4)使用上の情報(機械包括安全指針別表第5)
(1)~(3)の方策を実施して低減されなかった「残留リスク」に対して、メーカーはユーザーに「使用上の情報」として、「標識・警告表示」として機械に表示する、「警報装置」を設置する、「取扱説明書」を提供配布します。安衛則第24条の13の改正で、不明確であった残留リスクの情報を、機械危険情報としてユーザーに明確に伝達することが努力義務化されたことは前述の通りです。但し、本質的安全設計方策、安全防護又は付加保護方策が適切に適用できるにも関わらず、使用上の情報で代替することは厳に禁止されています。危険情報の内容については平成24年5月16日厚生労働省告示第132号「機械譲渡者が行う機械に関する危険性等の通知の促進等に関する指針」を参照して下さい。
なお「警報装置」はハード対策ですが、発せられた警報に人が気付いて、退避行動をとる等、2段階で「人に頼る方策」ですので確実性に劣るため「使用上の情報」の位置づけになっています。
ユーザーは、メーカーからの使用上の情報及び機械危険情報に基づきリスクアセスメントを実施し(1)~(3)の方策を実施しますが、最後に残った残留リスクに対して、「作業手順書の整備」「教育・訓練」を実施し、必要な場合に「個人用保護具」を使用させます。
(5)リスク低減に機械安全規格を活用しましょう
機械の安全化に関して機械包括安全指針は必須要求事項の大要を示していますが、実際に機械のリスク低減を図るには機械安全に関するJIS規格(ISO/IEC規格)を活用する必要があります。
4. 機械安全の人材育成
前述の厚労省告示第132号の第3条第1項に機械の危険情報は、リスクアセスメント、リスク低減方策、及び機械関係法令に十分な知識を有する者に作成させることとしています。平成26年4月15日付け基安発0415第3号により十分な知識を習得するためのカリキュラムが公開されました。
機械メーカーの品質保証管理者は設計技術者と同等の、ユーザーの安全担当者は生産技術管理者と同等の教育を受けることが望ましい、さらにメーカーの経営層、ユーザーの経営層・購買担当者についても上記の1.技術者倫理及び、2.関係法令について教育を受けることが望ましいとされています。
中災防では、教育通達に準拠した研修会を開催していますのでご活用下さい。
厚労省通達「設計技術者に対する教育カリキュラム」と中災防の機械安全研修の対応表
厚労省通達「生産技術管理者に対する教育カリキュラム」と中災防の機械安全研修の対応表
5. 機械安全化の支援
機械の安全化のため「公募型研修」「出張研修」「技術指導」を行っております。
詳しくはこちらから
6. 機械安全資料室
厚生労働省の委託を受けて中災防で作成した主な図書等です。